Stainless Steel Corrugated Tubes
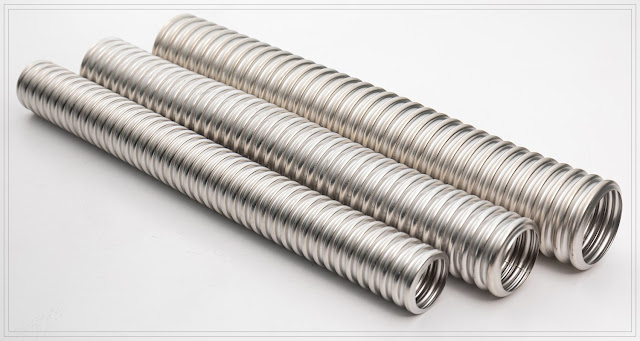
Stainless Steel Corrugated Tubes corrugated stainless steel tubing used for gas piping in buildings. Since 1990 CSST has been used within many buildings in both exposed and enclosed areas to install new gas system piping. The article discusses CSST uses, sources, installation specifications, and safety measures to protect the gas piping from damage by abrasion, puncture, lightning strikes or other hazards. Gas piping codes and industry sources of CSST are included. Our page top photo, provided courtesy of Carson Dunlop Associates, a Toronto home inspection & education firm, illustrates an improper installation of standard yellow CSST gas piping - routed in ground contact in a wet area. Yellow "Standard" CSST gas piping galso requires special electrical ground bonding to reduce risk of damage & leaks in areas of high lightning strike activity. Philips Metal is one of the renowned manufacturer, exporter, stockist, stock holder and supplier of a qualitative range of ...
Comments
Post a Comment